In early 2022 Reach Robotics was awarded funding from the Australian Government, Department of Industry, Science and Resources as part of their Australian Civil Space Strategy for 2019 – 2028. The ‘Moon to Mars: Supply Chain Capability Improvement Grant’ enabled recipient businesses to build their capacity to supply into the space sector. For Reach Robotics, the initiative facilitated the testing and development of our advanced manipulation systems for space environments, supporting Australia’s contribution to this sector and positioning for potential future projects.
Key applications of manipulator arms in space include On-Orbit Servicing (OOS) and Life Extension (LEX) servicing of satellites and other space craft. Conducting scheduled inspection and maintenance of satellites increases their operational lifespan and therefore improves their overall value.
A core division of our R&D team lead by Senior Electrical Engineer, Greg Molzen, began work on the ‘Moon to Mars’ initiative, optimising manipulators for complex space environments. The team were presented with a series of unique environmental challenges including ionising radiation, vacuum effects and extreme thermal fluctuations.
Over the duration of the grant, our team addressed each challenge through a process of testing, revision, and verification of our technology. Radiation testing was conducted at the Australian Nuclear Science and Technology Organisation (ANSTO), where our manipulators and electrical components were exposed to levels of radiation typical of space environments. This testing allowed our team to identify specific areas of improvement within our electrical components and informed future technical developments.

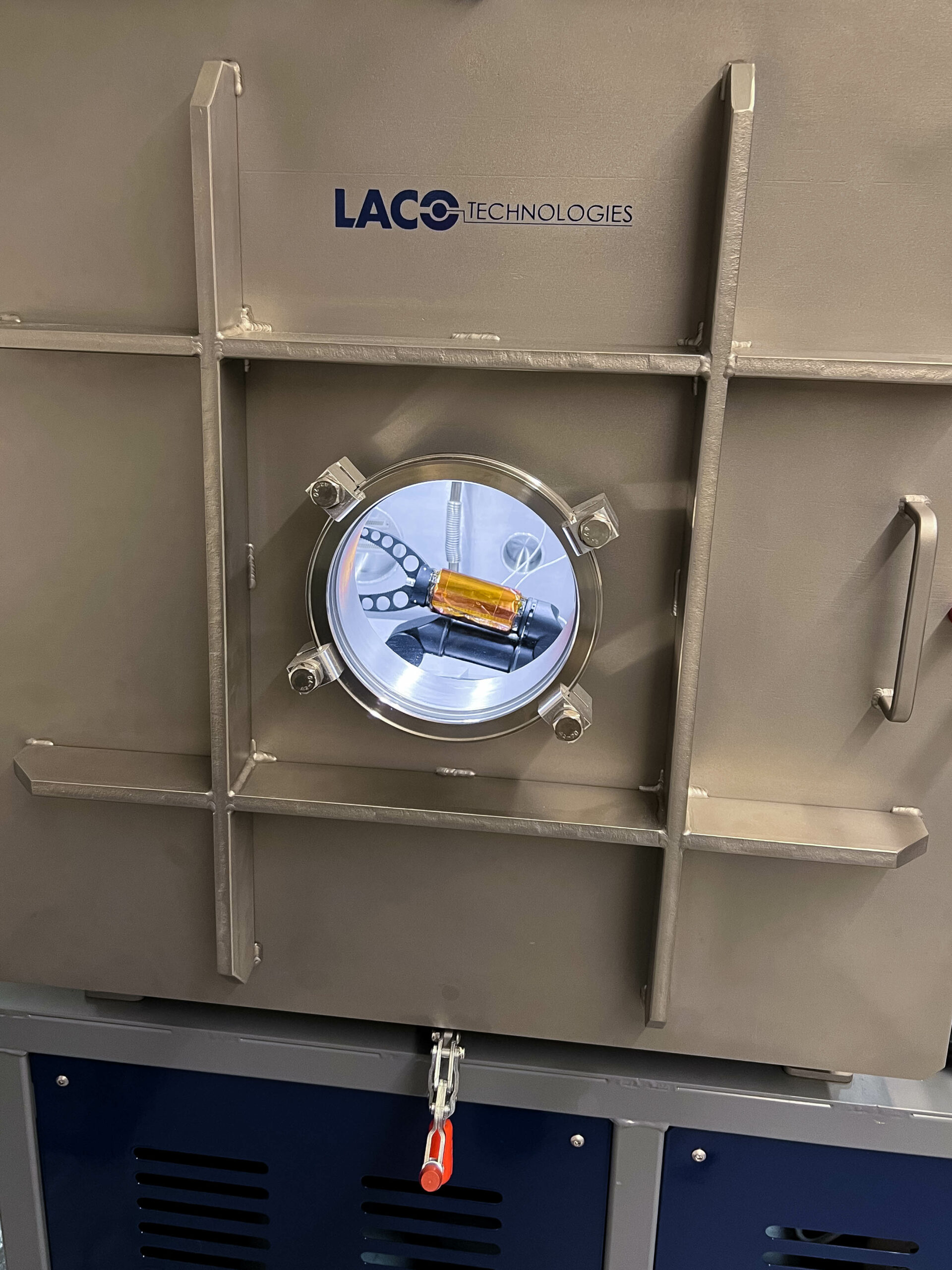
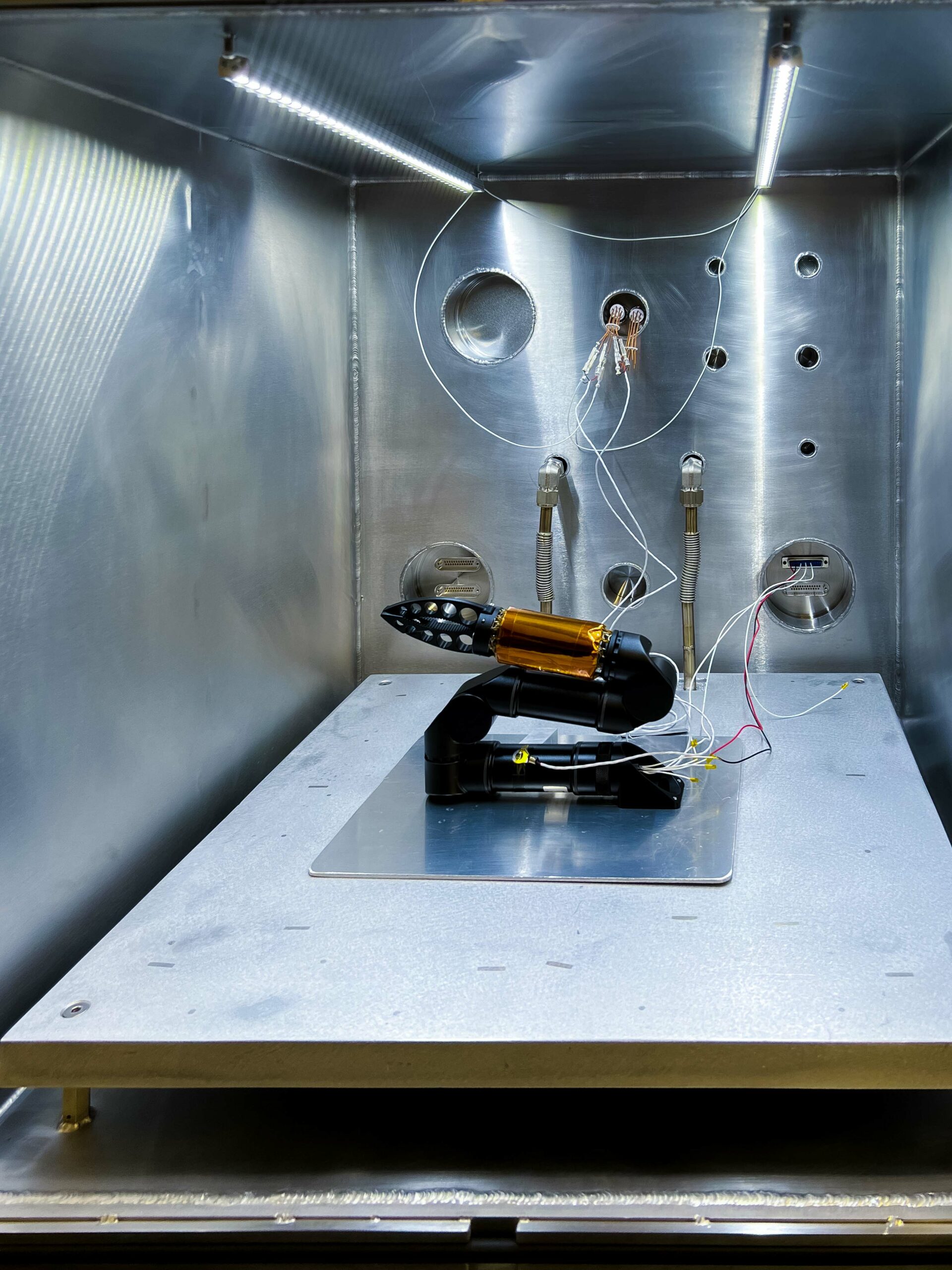
Thermal Vacuum Chamber Testing at UNSW’s Australian Centre for Space Engineering Research (ACSER)
Collaborating with UNSW’s Australian Centre for Space Engineering Research (ACSER), enabled access to the Thermal Vacuum Chamber at their state-of-the-art facility. A manipulator was placed inside the chamber where pressure and temperature can be adjusted to simulate the environment in space. Thermal Cycling Tests were completed at Vipac, subjecting the robotic arms to temperature rotations between -30°C – 60°C, imitating extreme thermal fluctuation. Further thermal verification was conducted in-house where manipulators were exposed to temperatures up to 110°C. These varied tests were critical in determining if the mechanical and electrical components of our manipulators can withstand the complexities of space environments without deterioration and with continued, reliable operation.
Additional challenges were faced concerning deployment specifications when launching space vehicles to avoid critical failures. Hikari Hashida, Mechatronics Engineer and significant contributor to our space research, elaborates, “there was increased complexity in optimising the system for high reliability during deployment and autonomous operation.” To overcome this, the manipulators underwent Electromagnetic Compatibility (EMC) testing and verification at Austest to ensure they did not produce electrical disturbance within a launch vehicle. The outcome of this verification process resulted in positive improvements to the electrical power subsystems in our manipulators overall.
Reach Robotics is proud to be identified by the Australian Government as a technical innovator in the development of remote operations for the space sector. We look forward to continuing to apply the knowledge and understanding gained of complex environments in further advancing our technology to withstand them.
