Robotics has been widely adopted by defence and security forces across the globe for the clearance and disposal of explosives. Remotely operated vehicles (ROV) or Unmanned Ground Vehicles (UGV) enable the operator to intervene, monitor and dispose of threats from a safe standoff distance, eliminating the need for bomb suits or other technologies that expose humans to potentially life-threatening situations. Similar technology is being trialled and adopted by first responders in dealing with fires, floods or more specific disasters such as malfunctions in nuclear or chemical plants.
Due to the unpredictability of emergency situations, the exact nature of the clearance task to be carried out is only loosely defined. The size, shape or weight of the threat is often unknown until a closer inspection can be obtained. Similarly, access into hazardous locations might be made difficult by fallen obstacles or confined entrance ways. It is therefore essential that the robotic solution can adapt to different conditions and operational challenges in-situ to ensure mission success in the shortest possible time.
The robotic arm, or manipulator with end effector tooling is a critical component of the intervention solution when it comes to conducting these types of operations. The ROV or UGV is a means of transporting the tool or sensor to the required location from which useful data can be obtained or intervention tasks can be carried out.

When a potential threat is detected, the operator determines which vehicle and tools best suit the task requirements with the limited information available. This decision is often made under severe time pressure and with little knowledge of the nature and conditions of the threat. The ability to select between multiple tools or end effectors prior to commencing is useful but often versatility around what can be achieved with the selected hardware is preferred. This allows for the manipulator to perform multiple operations such as cutting and grabbing without returning the UGV, saving valuable time.
If a different end-effector tool is required, it is essential the changeover process is fast and efficient and that a broad range is available with varied capabilities. Mission time can also be reduced by storing third-party tools on the vehicle and using a prototypical grabber style end effector to pick-up, hold and swap between them. Although simpler to implement, this method provides less versatility as the ability to actuate is lost when gripping.
As the use case for manipulator arms continues to expand it is important that the design of end effectors and tools is not undervalued. Reach Robotics has a growing library of versatile, mission-oriented end effectors for both Alpha and Bravo manipulator series. From cable cutters to grabber jaws of various shapes and functions, the array of interchangeable end effectors were designed with end-user application front of mind. Reach Robotics continues to work with customers in Land Forces and Critical First Response industries to meet their unpredictable application requirements.

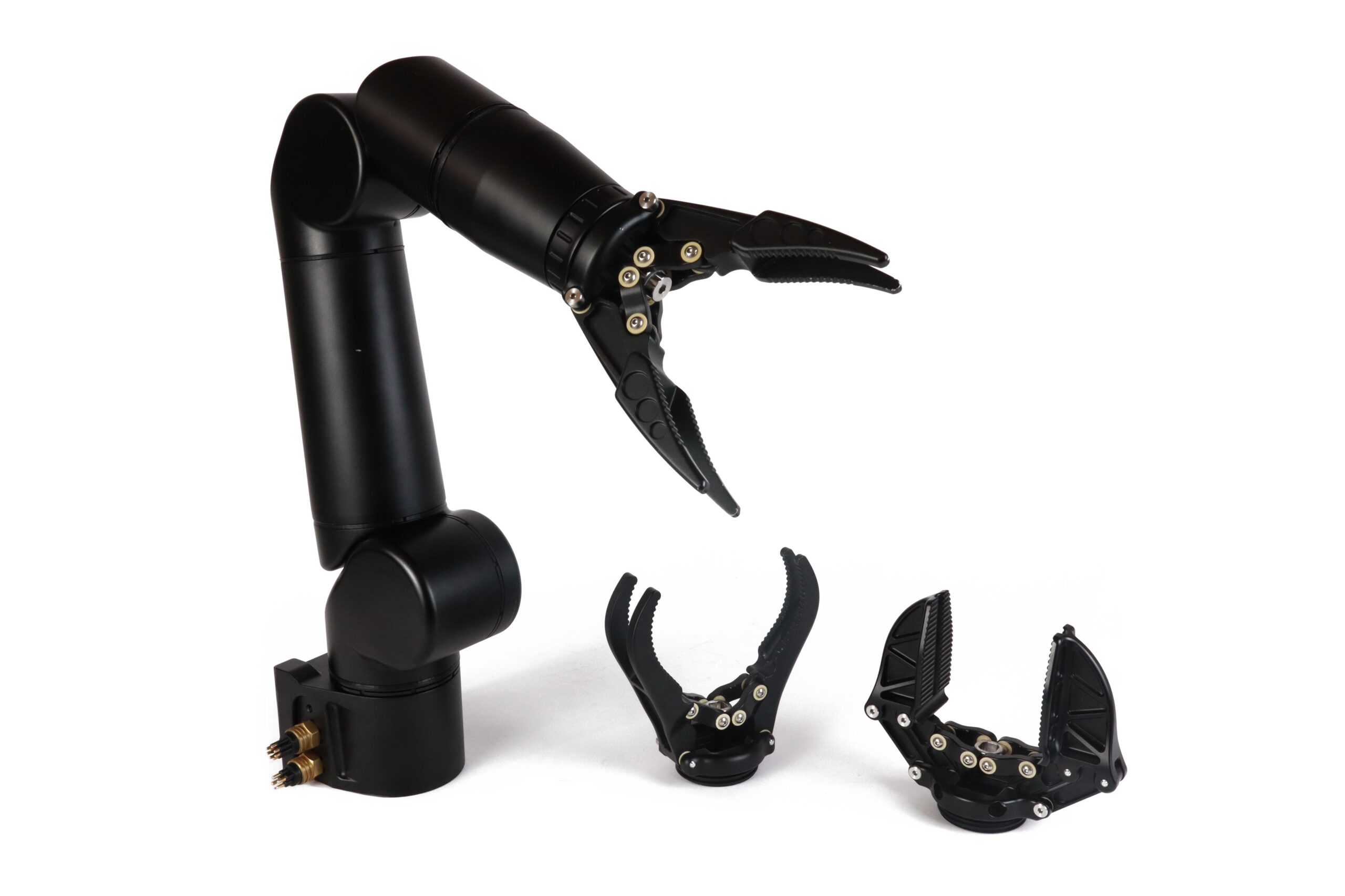